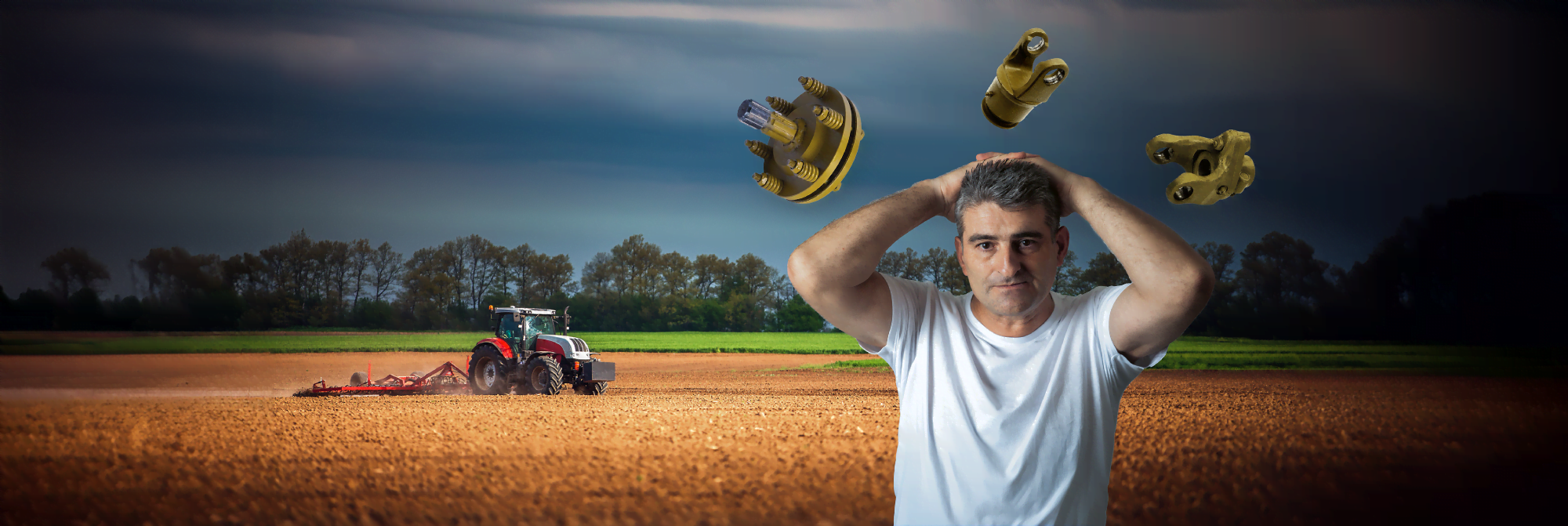
Types of couplings for PTO shafts - how to catch up in it?
The clutch transmits torque from the drive shaft to the driven shaft, in other words, it transmits drive from the tractor to another machine it moves.
The clutch, as part of the shaft, is attached with a cross-brace in place of the outer fork.
In addition, the coupling can come in the form of an adapter that allows the use of standard shafts without removing the forks. All you need to do is choose the right adapter and mount it on the machine.
Find out how unidirectional clutches differ from overload and friction clutches!
PTO shaft couplings – types
We can distinguish many types of couplings, which are used in basic and wide-angle articulated shafts.
-
Unidirectional couplings
They transmit torque in one direction. When there is a change of direction, or when the PTO drive shaft stops working, the clutch allows the machine to rotate freely by inertia until the rotation stops on its own, without damaging the drive’s working components. Unidirectional couplings are mounted to shafts that drive machines with a high moment of inertia, such as disc or flail mowers. They can be found in a right-hand variant for machines driven by the rear PTO shaft, or a left-hand variant for machines driven by the front PTO shaft.
-
Friction couplings
are able to transmit torque without disconnecting the drive when the overload reaches a set amount. They are used as a starting or overload clutch. A properly selected clutch protects the machine and tractor from mechanical damage to the drive components – the friction discs slip when the clutch exceeds the set maximum value. It is most often used for machinery subjected to rapid load changes, such as rotary harrows, flail mowers, disc mowers, soilers, balers, chippers or spreaders. In friction clutches, working components such as friction discs, springs and bolts are interchangeable which allows for longer and more efficient operation.
-
Unidirectional friction clutches
Are a combination of a friction clutch and a one-way clutch. They transfer torque without disengaging the drive when the overload reaches the size of the clutch setting, and at the same time allow torque transfer in one direction. They are used for machines that are subjected to rapid changes in load and yet have a high moment of inertia, including rotary harrows, flail mowers, disc mowers, soilers, balers and spreaders.
-
One-way friction clutches with disc spring
They can transmit torque without disengaging the drive and even when the overload reaches the size of the clutch setting; it also allows torque transmission in one direction only; they can be used in devices with high moment of inertia. Such a clutch can be found in a left or right variant.
-
Shear pin couplings
protect the components that transmit the drive from the tractor to the machine, in the event of an overload they interrupt the torque transmission of the machine. They disconnect the device from the tractor when the shear torque of the pin (in the form of a bolt) is reached. The coupling is reusable after replacing the bolt, but it must have the same strength parameters as the bolt used at the factory. Then the clutch will work normally again.
-
Ratchet overload clutches
protect the drive, automatically disconnecting it when the speed setpoint is reached. If there is an overload, the springs bend, disconnect the drive so that the clutch is not destroyed. Next, we look for the cause that resulted in the overload. Add that clutch failure can occur after only 20 seconds of overload operation.
-
Automatic overload clutches
Thanks to them, the drive can be interrupted if the value of the transmitted torque reaches a preset amount. In this case, it is not necessary to turn off the drive, immediately after the overload arises. Disengaging the drive with an automatic clutch does not wear out clutch components as with other types of overload clutches (pin, friction or ratchet). Once the resistance in the drive is removed, the clutch spontaneously restores drive transmission.
Which coupling to choose depends on the effect and protection you want for the machine’s working parts.
Two ways can be distinguished here:
- Frictional – in this case, springs and friction discs are used,
- Mechanical – it refers to the breaking of the safety screw, it is always necessary here to replace the screw with a new one before returning to work.
It is always a good idea to read the instructions of the machine to which you want to apply the workpieces.